THE CHALLENGE
Re-design human-robot interaction to achieve a real collaboration in an
industrial environment.
By achieving this collaboration, robot efficiency increases and industrial
processes improve.
The technical potentials of robots are exploited, and
qualitative human skills are value in order to create
the best industrial conditions.

OUR SOLUTION
CoEx is a bidirectional communication system which introduces the foundation for a proper collaboration between humans and industrial robots creating a new common language. Communication is indeed fundamental to enable
collaborative processes, because it establishes the relational codes that
allow the two parts of a relationship to understand each other and to do
something together efficiently.
This new communicational dynamic helps the operator and the cobot (collaborative robot) understand each other without necessarily making one adaptable to the other, but giving them a common language of interaction,
thus mutual comprehension.

COEX
WHY is it needed?
Imagine yourself working with an alien whose body language and communication means are intrigued and ambiguous. How could you even dream to collaborate without comprehend each other?
Of course it’s really hard, that is why our solution aims to make operators feel comfortable working with cobots, while at the same time to make these last able to recognize people and act accordingly to work more efficiently mantaining safety.
HOW TO DO THIS?
Our “alien” is a mobile collaborative robot surfing around the industrial plant, and thanks to CoEx it has a new communicative code expressed through a new operators-friendly interface that can show them what the cobot is doing and which areas they should avoid. At the same time, CoEx makes the cobot able to see you, this way it is possible to avoid interfering with one another.
WHAT IS IT COMPOSED OF?
CoEx aims to improve the whole working experience and process flow.
It consists in a 5-points system made by:
-
Two light projectors mounted on the robot sides can visually show the warning and danger areas. In these areas operators could get hit and cobots would slow down its workflow if something is detected inside.
-
A vibration/light enabled wearable device that alerts you when you are too close to the robot.
-
A ultra-wideband (UWB) localization system that makes the robot aware of operators’ position.
-
A Kinect vision system which recognizes operators' main joints.
-
A cloud network that connects and coordinates everything together.
​
Let's know them in detail.
LIGHT PROJECTORs
LG HF65LSR
​
-
Ultra short throw projector
-
1000 lumens
-
Ideal compact design
​
The projector shows on the industrial floor the areas around the cobot that could jeopardise operators' safety and the efficiency of the whole industrial process.
​
​
​
Projecting the warning areas and the danger areas, we make the operator aware of them and we help him avoid passing through those zones, in which if the cobot detects something it slows down or completely stops.
​
​
​
The projector also shows another information: the indication of the task currently executed by the cobot. This information helps the operators understand what the cobot is doing and is going to do.
​
​
​
Lastly, the projector shows tangibly the detection operation of its detection system. If one operator is detected a dot that follows him will appear on the border of the warning area. This dot expands when the operator approaches and becomes smaller when he walk away.

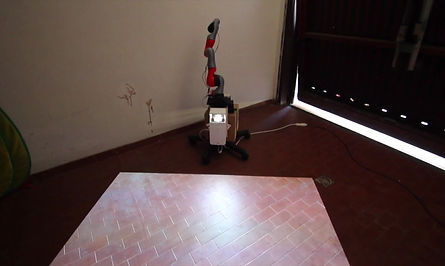
Wearable device
This wearable device is composed of a vibration motor and LED lights that are meant to alert operators, and a microcontroller that receives the activation order from the cloud network and commands the vibration motor and LED lights.
This wearable device is activated when operators are about to enter the cobot's warning area. It is particularly useful in situations where operators are not aware of their surroundings, for examples when they are not facing the cobot, or when they are not paying attention.​
​
Thanks to this wearable device, operators “feel” and “see” the danger in any situation.
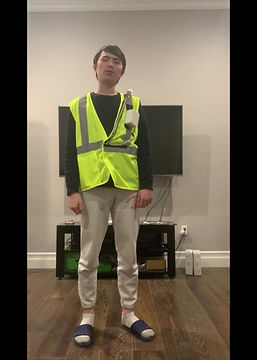
UWB System
UWB (ultra-wideband transmitter/receiver )
​
-
Flexible system: it can be adapted to every industrial
environment -
Good beacons' detection precision
​
This indoor localisation device permits to track operators positions in the plant in relation to the cobot's position

Kinect VIsion system
Kinect
​
-
Recognition of human shape by the detection of
human joints -
Good precision in tracking people nearby
​
This device permits the recognition of the operators once they are near the cobot and also permits to understand if the operator is facing the cobot or not.
​
​
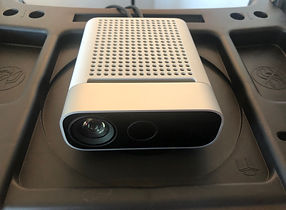
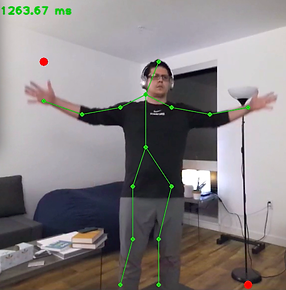.png)
cloud Network
This is something invisible but fundamental for the construction of our system. It represents the invisible connection among all CoEx components: humans, cobots, light projectors, UWB system, Kinect system, and wearable devices.
​
Thanks to our cloud network, we can call what could be just a set of components, a real system!