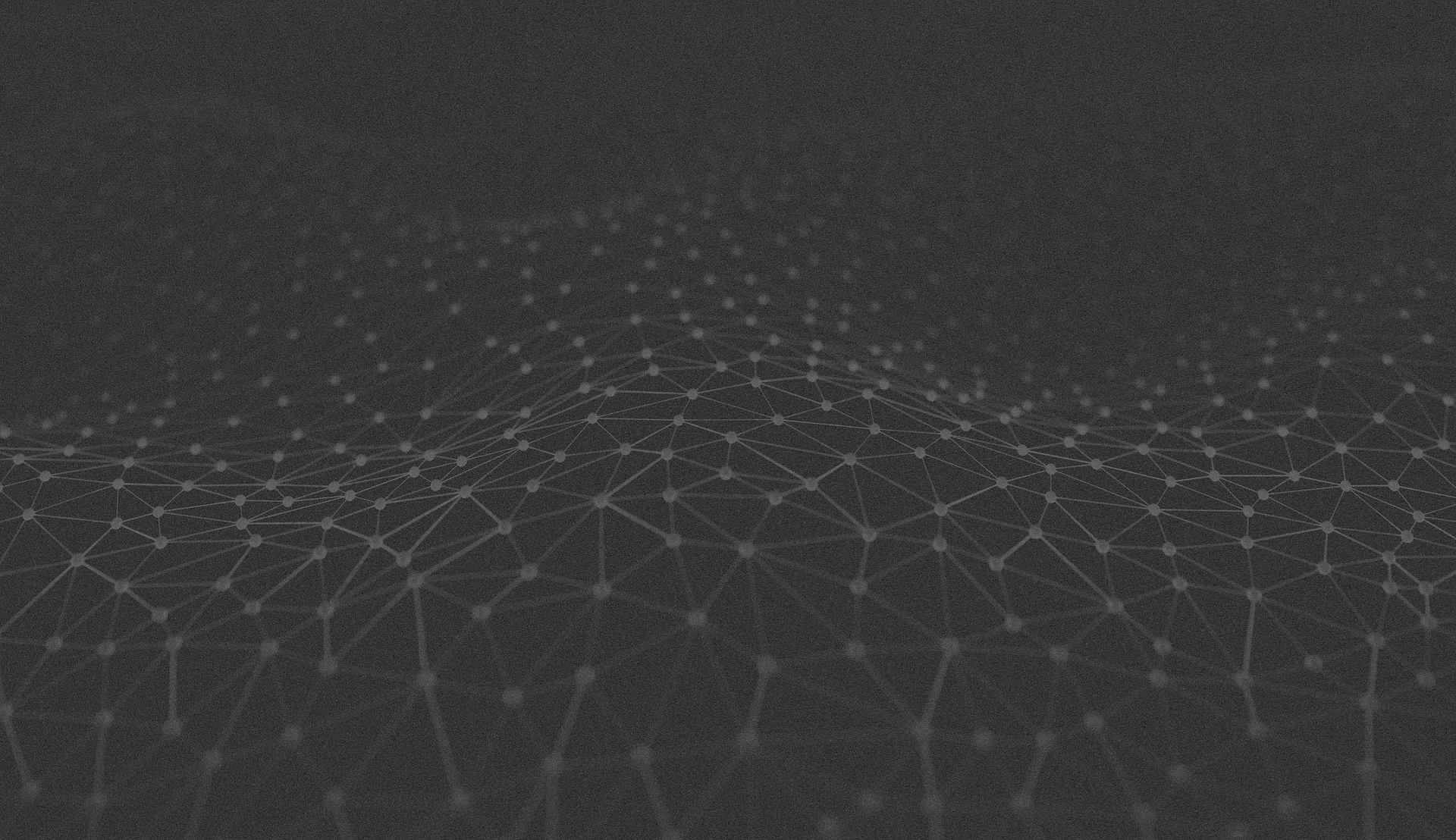






_pn.png)
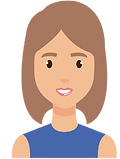


Final
Prototype
Design Space
Exploration
Critical Function
Prototype
Funky
Prototype
Dark Horse
Prototype
Functional
Prototype
X-is-finished
Prototype

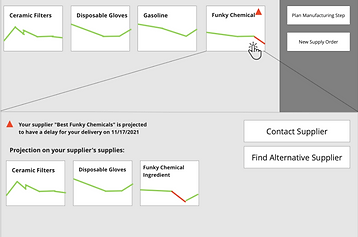


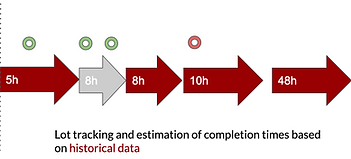

At the beginning of our project, we barely knew anything about the journey from the patient to the donor, plasma-derived therapies, nor pharmaceutical manufacturing. We started benchmarking, desk research, and interviews to determine where silos and communication gaps exist and what a control tower is all about.
Analyzing Takeda’s organizational structure, we identified several stakeholder relations that may be susceptible to communication gaps: All stakeholders need different complexity and real-time data availability, making it difficult to create a view that fits all. Therefore we experimented with different levels of granularity and visualization of process data.
In the Dark Horse Phase we build prototypes that take an unusual perspective on the user’s problems and needs. This phase aims to diverge into unchartered territory rather than focus on the feasibility of the individual prototypes. One idea: Improve the plasma data by tracking people’s workout behavior using an app.
In the Funky Phase, we build prototypes that combine different aspects of previous prototypes. This phase aims to start to converge towards more concrete and more fleshed-out prototypes to test out combinations of different experiences and functions.
In the Functional phase, we came up with our vision: Every employee has understandable information to make informed decisions and track down problems.
We came up with a targeted architecture for the prototype and built our solution’s core components.
As part of the X-is-finished prototype, we refined our architecture, focussing on functionality for the supply chain manager role to display the estimated arrival times of the current lots in the manufacturing process.
For the final prototype, it is really about building the product. We reorganized our team into subteams working on different parts of mapd, set up a scrum workflow, and introduced project management software. While still working on our final product screens, we started implementing and deploying our solution live. To get feedback, we used intense co-c creation sessions with employees from Takeda.

Explore all of our prototypes from the different phases in our prototype booklet
Towards
Our Challenge:
How might we design a Control Tower within Factory of the Future for the Plasma Operational Unit to overcome silos and communication gaps of involved stakeholders, based on academic / cultural background and different understanding / views on data, to ensure effective operations within the entire organization?